Slot Die Coating Head Design
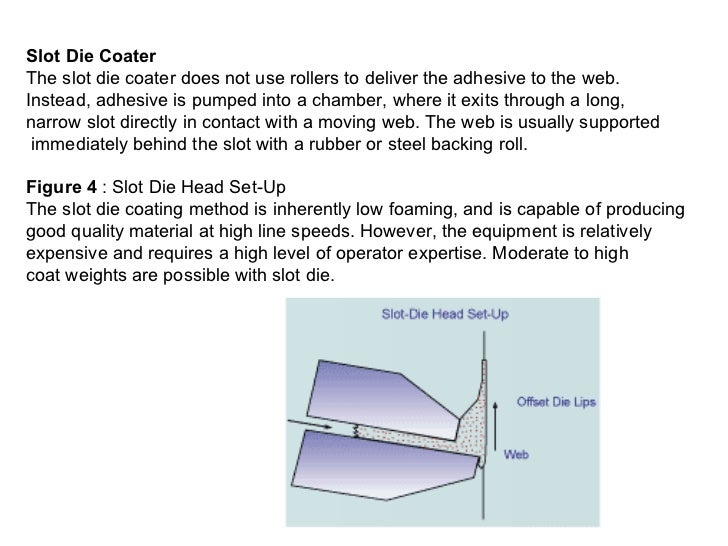
In this video, Tapemark Engineer Mike Rothaupt compares and contrasts slot die coating with comma head coating. We offer both here at Tapemark, and we have t. The slot-die heads intended for operation at low pressure with low viscosity inks are comprised of only two parts which greatly simplifies assembly, disassembly and cleaning. They can be operated with a single shim or with a shim kit comprising shim and meniscus guide for coating stripes at low web speeds (0.1-5 m min-1).
Slot Die Coating is a highly scalable technique for rapidly depositing thin and uniform films with minimal material waste and low operational cost. Slot Die Coating technology is used to deposit a variety of liquid chemistries onto substrates of various materials such as glass, metal and polymers. This is achieved by precisely metering the process fluid; dispensing it at a controlled rate while the coating die is moved relative to the substrate.
Slot Die Coating has historically been used in industry scale manufacturing due to its reliability, high throughput, and extremely low waste production. The patent for Slot Die Coating first principles was filed by Eastman Kodak Co. in 1951 for the production of photographic films. Today, some of the world’s most important commercial products are made using Slot Die coating techniques. This includes LCD displays, chemical release patches, touchscreens, food packaging, Li-ion batteries and multi-layer ceramic capacitors among many other applications.
Slot Die Coating Head Designer
Slot Die systems achieve their coatings by delivering the desired coating fluid (often referred to as “ink”) onto the substrate through a highly precise delivery component known as the “Slot Die head.” The Slot Die head lies at the core of any Slot Die Coating system. Its design and position relative to the substrate significantly influence the quality and stability of the resulting thin film.

A fully assembled Slot Die head consists of several key components. Namely, the front plate, back plate, shim, and meniscus guide. The front and back plates are the exterior metal blocks that receive the ink from the delivery system and secure all of the Slot Die head components in place. The shim and meniscus guide are two thin sheets of metal between the front and back plate that serve to guide the ink to the coating edge of the Slot Die head.
The interior design of a Slot Die head can vary. Typically, the ink is pumped into the system via tubing connected to an inlet on either the front or top of the Slot Die head. Upon entering the Slot Die head, the ink first fills into a hollow cavity that has been machined into one of the Slot Die plates. This cavity is often referred to as the ink reservoir, manifold or distribution chamber. The ink is then guided downwards from this reservoir to the coating edge of the Slot Die head by the shim, whose cutout shape determines the coating width or stripe pattern of the ink on the substrate. A meniscus guide may sometimes be used to stabilize the fluid meniscus between the Slot Die head and the moving substrate. The meniscus guide typically appears as a metal tooth protruding from the bottom lips of the Slot Die head, facilitating the flow of the ink out of the Slot Die head and onto the substrate.
A key benefit of Slot Die Coating is its “pre-metered” nature. This means that the coated wet film thickness (t) can be easily controlled and calculated from the pump rate (Q; the rate at which ink enters the system), the substrate motion speed (U; the rate at which the substrate accepts ink from the system), and the coating width (W; the width across which the ink is dispersed upon the substrate. Not shown in schematic).
Unlike in “self-metered” coating techniques, the height of the Slot Die head does not physically control the thickness of the coated layer. Instead, the wet layer thickness in Slot Die Coating is entirely determined by the volume of ink applied to the substrate, divided by the area over which the ink is coated. This affords a highly flexible, “contact free” coating process, with additional benefits such as closed fluid delivery and wide viscosity compatibility (up to tens of thousands of cP). These properties combine to provide significant process control and scaling advantages over common R&D coating techniques such as blade coating, bar coating and spin coating.
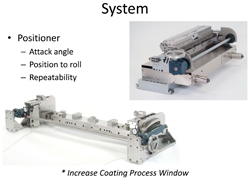
Slot Die Coating Head Designs
Coating thickness is often the primary parameter of interest for users of Slot Die coating equipment. However, control over the quality of this coating must also be carefully considered. The quality of coating is generally discussed in the context of the “stable coating window” of a process. This stable coating window is defined by all of the possible combinations of upstream pressure versus the gap-to-thickness ratio that result in a stable meniscus without defects in the final coated layer (e.g. ribbing, pinholes, etc.).

In practical terms, achieving a defect-free film of a desired thickness is often a matter of simply balancing the ink pump rate, substrate motion speed, and slot die height against each other. However, the boundaries of the stable coating window can also be influenced by the position of the Slot Die relative to the substrate, as well as the nature of the inks and substrates being used. Viscosity, surface tension and surface energy are just a few of the material properties that can be controlled and optimized together with high quality Slot Die hardware and motion systems to achieve ultra-thin films with outstanding uniformity. By controlling these parameters, Slot Die Coating provides precise, repeatable and scalable thin films with thicknesses ranging from tens of nanometers to hundreds of microns.
Slot Die Coating has seen a great increase in lab-scale R&D applications in recent years, as researchers strive for more consistent experimental results and rapid scaling of new additive manufacturing processes to roll-to-roll and sheet-to-sheet production. As a result, FOM Technologies coating equipment is now supporting cutting edge research into 3rd generation solar cells, OLED and electrochromic devices, fuel cells, batteries, sensors, membranes, printed electronics, medical diagnostics, conductive thin films and more.
At FOM Technologies we aim to bring industry-grade coating solutions to the R&D environment. We pride ourselves on providing high quality hardware, user-friendly process control, and a researcher-focused design mentality across all of our products. Whether you are conducting fundamental research, establishing a pilot process, or moving into full-scale production, it is our mission to support you with a premium, precise and scalable Slot Die Coating platform to elevate your thin film research and production projects.
For a more detailed discussion of Slot Die Coating and a comparison with similar technologies, see our Slot-Die Coating: Introduction & FAQ document.
FIND US
FOM Technologies
Artillerivej 86, 1.
2300 Copenhagen S
Denmark
Company nr: DK 34715726